Part Three
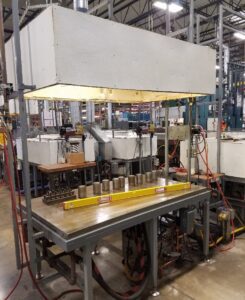
Water-based hot table with insulated cover and winch/pulley lifting mechanism.
Quick recap: the Molded Dimensions Team earned best technical paper for their work as the Urethane Restoration Team. The Team sought to find the root cause of the amount of scrap that was being produced each week at Molded Dimensions. We talked last week about the problem. Then, we talked about the strategy. Now, we’ll talk about our next finding: temperature variation matters.
Temperature Variation Matters
At MDI we heat molds with either hot tables or ovens. We also have hydraulic presses where we compression mold parts. We found that a disproportional amount of our scrap was from our hot tables rather than the ovens. The oven temperatures were consistent, the hot tables were not. The team took a closer look at our large electric hot tables. After trying several different types of electric heating elements with limited success and scanning the marketplace for other commercially available options, the team was stuck.
Not willing to settle for small improvements, the team decided to design a water based hot table that was heated evenly through a custom designed hollow platen. The result was groundbreaking, allowing for less than two degree variation in temperature across the tables. Over the next few years MDI replaced all flat electric heating elements with the new proprietary design.
In addition, many of our hot table covers were leaky and ineffective at maintaining heat because they were broken. After asking “Why?” several times, the team learned the covers were very heavy and unwieldy and easy to accidentally damage, so they added a pulley and winch system to lift the covers. The team also insulated the inside of the covers to better retain heat. Now they don’t break, so heat is consistently maintained, and equally importantly, the operators have a much easier time using the covers.
The team reduced temperature variation in our compression molding area by adding water based hot tables in front of each press so that mold temperatures stayed consistent during demolding, mixing, and pouring. For the presses which are still heated using electric heating, we did an audit to ensure that the wattage of the electric heater rods were consistent within each platen and from press to press (they weren’t!) and also completed controller tuning to ensure that the heat was maintained in as tight a window as possible. We also experimented with electric heater wattage to determine the optimum: lower wattage heaters responded slower than higher wattage heaters, but didn’t have as extreme min/max spikes. Once we decided which was better, if a press didn’t match, the platen heaters were converted at their next refurbishment.
Finally, in addition to our traditional contact pyrometers we began using infrared temperature gages so that the operators could verify the temperature of our resins prior to mixing, to ensure that they had been preheated to the correct specified temperature.
Join us next time for our second discovery: Flatness matters.