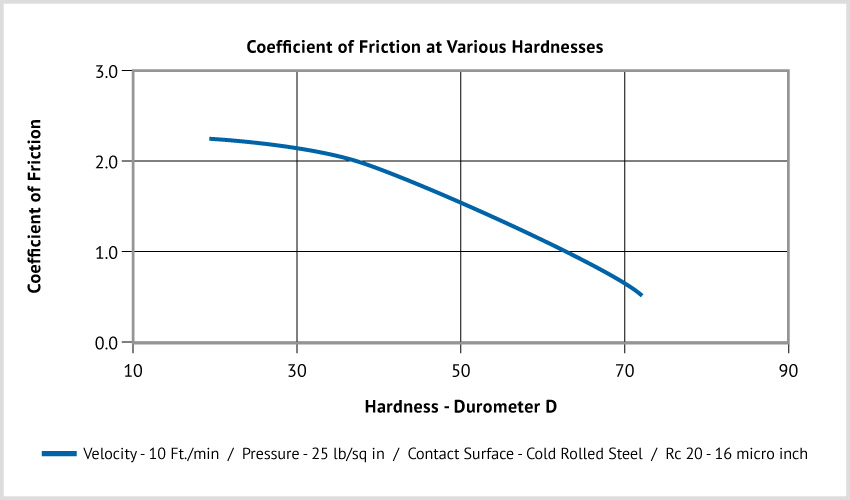
Figure 1
Friction of urethane polymers against non-lubricated surfaces decreases with increasing hardness of the polymer, as shown in Figure 1. Because harder polymers have the lowest coefficient of friction, these materials are used when sliding resistance is important. This characteristic, coupled with both its superior abrasion resistance and its load-carrying ability, are important reasons why urethane is used for bearings and bushings. Since the hardness of urethane compounds approaches that of some plastics, comparison of urethane with various plastics is shown in Table I.
Effect of Additives on Friction Properties
Additives may be used to alter the frictional proportion of urethane polymers. With urethane, powdered Teflon® TFE fluorocarbon resin and Teflon® TFE fluorocarbon fiber flock significantly reduce the coefficient of friction of this elastomer. Alternatively, the incorporation of graphite increases the coefficient of friction. The frictional change due to these additives is shown in Figure 2. Urethane without additives is used as a control.
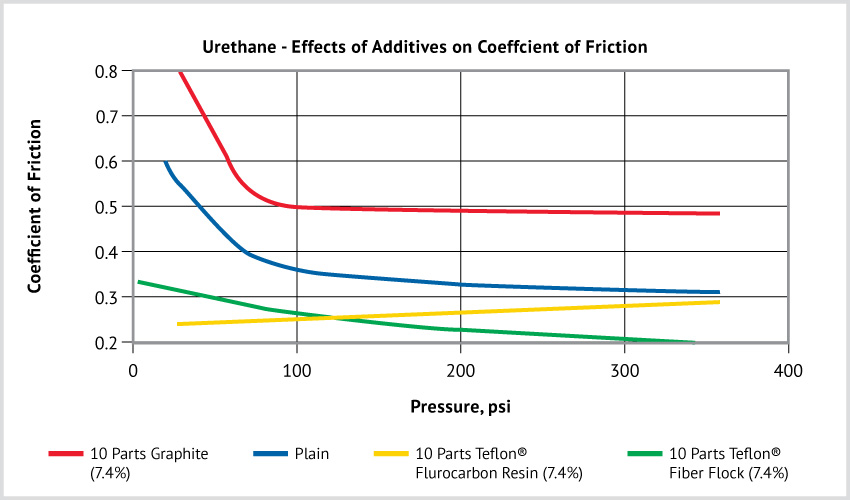
Figure 2
The aforementioned additives will also affect other physical properties of urethane. These property changes are presented in Table II.
All additives at a 10-part level (7.4% by weight of total compound) will reduce modulus, tensile, and elongation. Additives that reduce the friction coefficient also improve abrasion resistance. The improvement in abrasion obtained with the addition of Teflon® fluorocarbon fiber is significant and was also observed during long-term friction tests.
A level of 10 parts additive is not necessarily the optimum. However, a 10-part level offers significant frictional improvement over 5 parts and is not significantly inferior to 15 parts. The optimum level of additive, considering a balance of physical and frictional properties, probably falls between 5 – 10 parts.
Effect of Additives on Bearing Performance
Both graphite and Teflon® improve the performance of urethane in bearing applications. Even graphite, which results in an increased friction coefficient, will provide better bearing service. This unexpected improvement is likely due to the eventual formation of a graphite film at the load interface, and also to the better thermal conductivity of the graphite-filled compound.
Pressure-Velocity (PV) limit data for bearings based on urethane, Nylon 66, and Delrin acetal resins are shown in Figure 3. These curves represent the performance limits of the bearings. Bearings can operate without catastrophic failure at any combination of pressure and velocity below the respective curves. The PV limits predict nothing about the length of service, however. Although urethane may be expected to outwear most thermoplastics, its performance will be influenced strongly by temperature and other environmental conditions. The best determination of bearing durability is a service test.
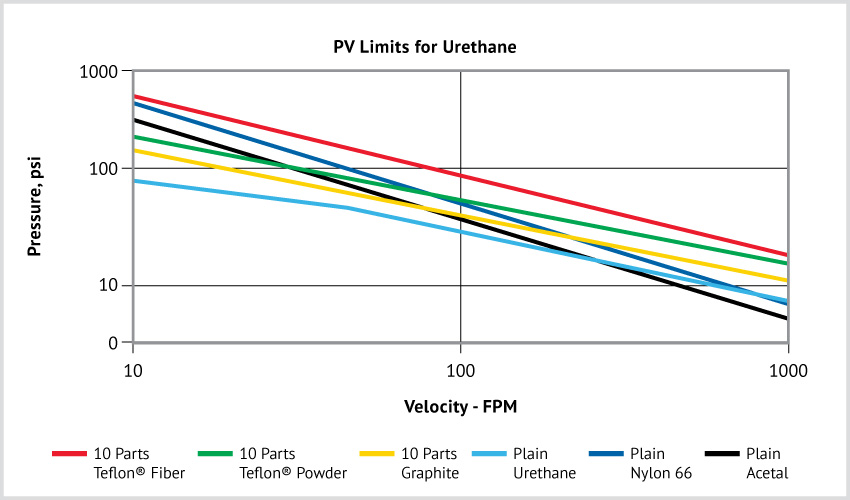
Figure 3
Access more articles in our Urethane Knowledge Center.