Tensile strength and ultimate elongation, while extremely useful for compound development and control, are of lesser importance to the design engineer. Elastomeric parts are seldomly loaded in tension, and even then, only to a small fraction of their ultimate strength. Tensile strength and elongation generally cannot be correlated with performance in service. The relationship of stress to strain is more useful, because it shows how an elastomer responds to loading.
Tensile properties are measured by recording axial stress in a standard ASTM dumbbell specimen at a constant rate of strain. Tensile strength, elongation, and modulus, as applied to rubber, are defined as follows:
- Tensile is the force per unit of the original cross-sectional area that is applied at the time of a specimen’s rupture.
- Elongation, or strain, is the extension between benchmarks produced by a tensile force applied to a specimen. Elongation is expressed as a percentage of the original distance between the marks. Ultimate elongation is the elongation at the moment of rupture.
- Modulus is the stress in pounds per square inch, of the original cross section, required to produce a certain elongation.
If a tensile stress of 1800 psi produces an elongation of 300%, the compound is said to have a ‘300% modulus of 1800 psi.’ In rubber—unlike steel—stress and strain in tension are not proportional; therefore, the term modulus has a different meaning. When applied to steel, modulus means stress at a certain strain—not a ratio and not a constant, merely the coordinates of a point on the stress-strain curve.
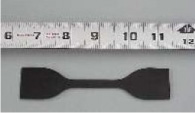
FIG 1
Procedures for conducting stress-strain tests are standardized and described in ASTM D-412. Dumbbell-shaped specimens 4-5 inches long are die-cut from a flat sheet, and then marked in their narrow section with benchmarks 1-2 inches apart (FIG 1). The ends of the specimens are placed in the grips of a testing machine (FIG 2). The upper grip is power-driven at 20 inches per minute, and it stretches the specimen until it breaks. As the distance between benchmarks widens, measurement is made between their centers to determine elongation.
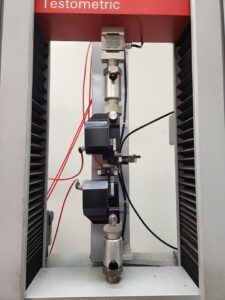
FIG 2 – Testing Machine
Stress-strain properties are useful in compound development and for manufacturing control. As control tools, stress-strain properties reveal whether the ingredients have been mixed properly, or if contaminants are present. Property changes by environmental conditions are easily detected by a shift in stress-strain properties. For a product that has been put in production, modulus and elongation measurements can be used as quality control tools. They are sensitive to manufacturing variations and indicate if the product has been properly processed.
Tensile stress-strain curves for compounds of urethane are shown in Figure 3. The tensile strength of commercial compositions of urethane will vary from 2000 psi to over 11,000 psi. Elongation will vary from 250% to 800%. Generally, tensile strength increases with an increase in hardness.
Figure 3 also shows that urethane elastomers retain extensibility at high hardness. Elongation at a break of 75 durometer D, achieved with urethane, is usually 250%.
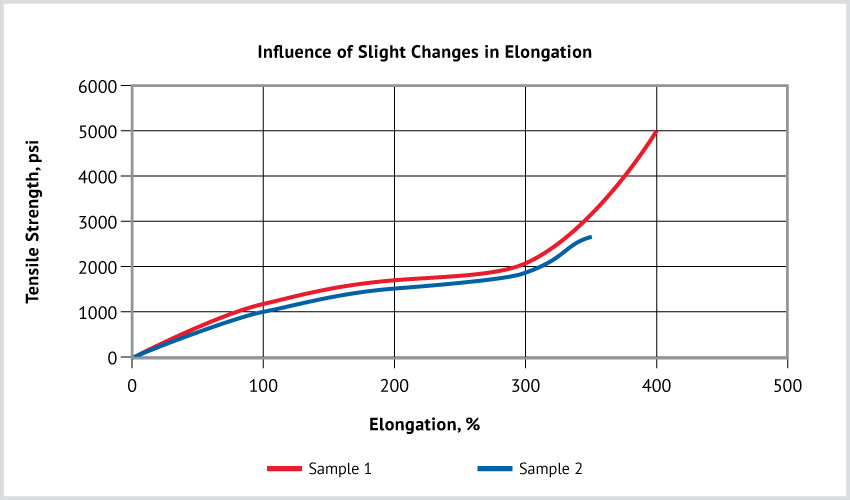
FIG 3
The response of materials at low moduli is more important to the design engineer than the ultimate tensile strength. As shown in Figure 4, tests from the same material can yield widely varying tensile strengths, simply due to small differences in elongation. In this case, an elongation at a break of only 50% can result in a 2200 psi change in tensile strength. The variability in tensile strength can be caused by small voids in the specimen or small invisible nicks in the sample. Stress at 100% modulus yields very consistent results that are reproducible, compared to other tensile properties.
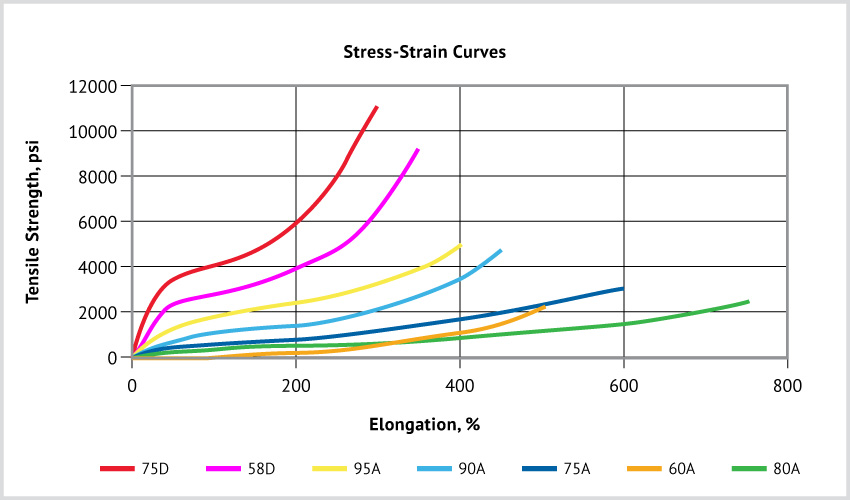
FIG 4
Access more articles in our Rubber Knowledge Center and our Urethane Knowledge Center.